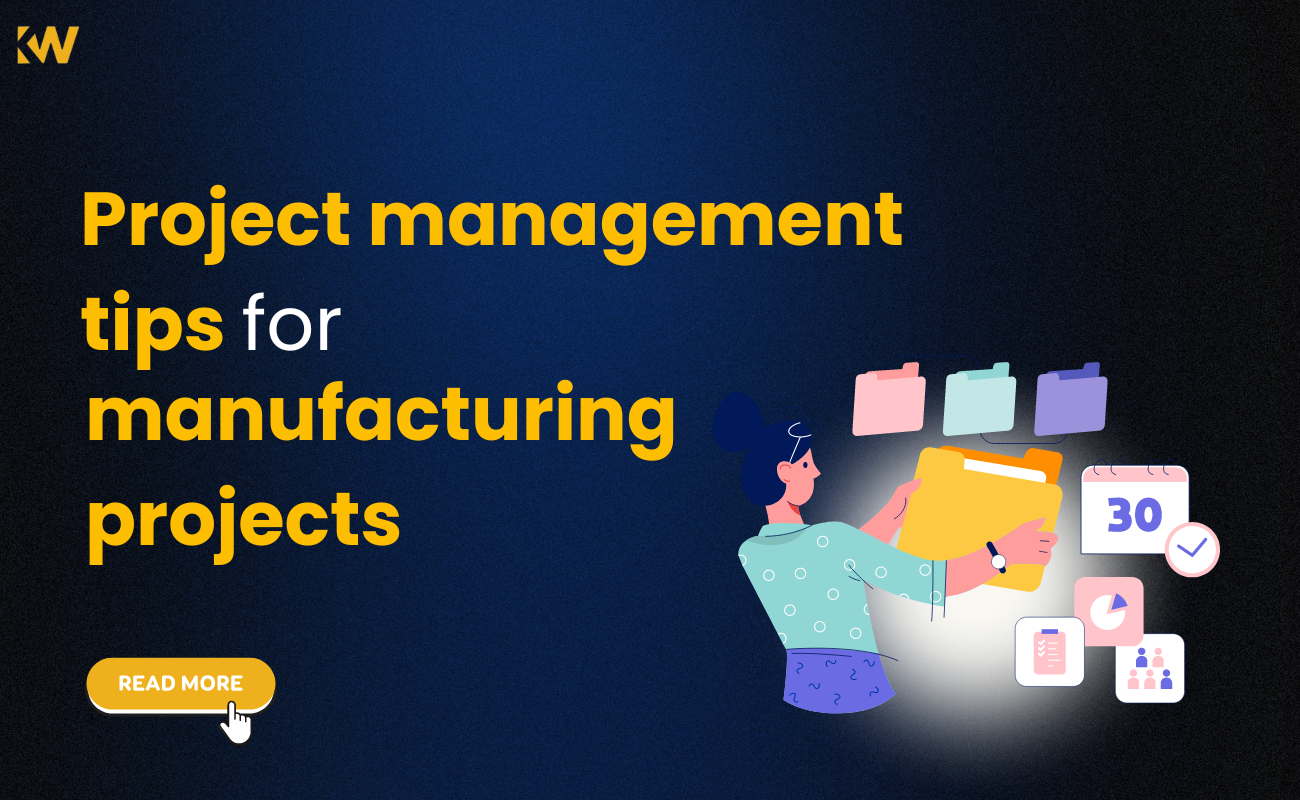
Project management tips for manufacturing projects
Posted On September 24, 2024 - 12:45 PM
Project management in the industrial sector is complicated and comes with a certain set of criteria. Large teams, stringent deadlines, complicated supplier chains, and regulatory requirements are all common in manufacturing projects. In this field, efficient resource management, strict adherence to budgets, and preservation of quality are all guaranteed by effective project management.
Project management concepts may optimize manufacturing processes, upgrade equipment, or create new products while streamlining the process and reducing risks. To help project managers overcome typical roadblocks and produce effective results, this article examines essential project management advice that is especially suited for manufacturing projects.
1. Recognize the project's goals and scope
Clearly defining the project's goals and scope is the first step towards a successful manufacturing project. This might entail determining the exact product specs, production needs, and end goals for manufacturing.
-
Clearly define your objectives by dividing the project into SMART (specific, measurable, attainable, relevant, and time-bound) goals.
-
Clarity of Scope: Clearly state what is and is not part of the project. This is crucial. By doing this, scope creep—the addition of new work without sufficient preparation or funding—is avoided.
-
Align Stakeholders: Ascertain that all parties involved—production managers, suppliers, engineers, and quality control—are in agreement. Unrealized expectations may cause delays or problems with quality.
2. Give planning and scheduling top priority
Any successful manufacturing project is built on planning. Manufacturing, in contrast to software initiatives, frequently faces logistical challenges, supply chain intricacies, and physical limitations that call for careful preparation.
-
Gantt charts: To plan out tasks, deadlines, and dependencies, use Gantt charts or other visual tools.
-
Resource Allocation: Before the project commences, make sure that labour, equipment, and raw materials are available.
-
Determine Crucial Routes: Determine which activities have a direct impact on the project schedule and make sure they are prioritized.
-
Having a well-thought-out strategy can also help you to foresee obstacles and create backup plans to minimize risks.
3. Apply the Principles of Lean Manufacturing
Lean concepts are very useful for managing manufacturing projects because they put a strong emphasis on cutting waste and increasing efficiency. By promoting a culture of continuous improvement, these guidelines guarantee that the project operates effectively with fewer delays and cost overruns.
-
Value Stream Mapping: List all of the steps involved in the manufacturing process, from obtaining raw materials to delivering the finished product, and eliminate any steps that don't contribute value.
-
Kaizen, or continuous improvement, is the practice of encouraging staff members to make small adjustments to their work to improve project outcomes as a whole.
-
Just-In-Time (JIT) manufacturing minimizes inventory costs and prevents overproduction by only producing what is required when required.
4. Wherever possible, use agile methodologies
Despite having its roots in software development, agile may be used to manufacturing projects, especially in the design and prototyping domains. Agile encourages adaptability, teamwork, and incremental improvements—all of which are beneficial in the rapidly changing industrial environment of today.
-
Scrum Framework: For handling complicated projects like redesigns or equipment upgrades, use Scrum. Breaking the project up into sprints, this method makes it easier for teams to adapt to changes and concentrate on short-term objectives.
-
Feedback and Collaboration: Agile fosters ongoing communication and cooperation across departments and teams, guaranteeing that any modifications or enhancements are applied without impacting the project's overall schedule.
5. Pay attention to quality control
The quality of the product is crucial in production. Inadequate quality control might result in expensive delays, recalled products, or disgruntled customers. Any manufacturing project must have a strong quality control system in place.
-
Total Quality Management (TQM): This strategy places a strong emphasis on ongoing process and product improvement. You can find and fix problems early on in the project by integrating quality into every stage of the process.
-
Six Sigma: This approach seeks to reduce variances and flaws in the manufacturing process, guaranteeing that the final product lives up to consumer standards.
-
Automated Quality Testing: To increase precision and lower human error, use automated quality checks whenever practical.
6. Risk Control Is Essential
Manufacturing projects are vulnerable to a range of hazards, including unanticipated regulatory changes, supply chain interruptions, and equipment failure. Putting in place a strong framework for risk management will guarantee that you are ready for these obstacles.
-
Identification of Risks: Enumerate possible hazards that can affect the project, such as malfunctioning equipment, a lack of supplies, or failure to comply with regulations.
-
Strategies for Mitigating Risk: Create backup plans in case of high-probability events. For instance, arranging for regular maintenance for vital equipment or having backup providers.
-
Frequent Evaluations of Risk: Risk management has to be a continuous process that involves periodic evaluations to evaluate emerging risks and modify mitigation strategies.
7. Make Automation and Technology Investments
With the advent of Industry 4.0, several technological advancements have been made that can improve the way industrial projects are managed. Process optimization, precision, and a decrease in the need for manual intervention are all aided by automation, robots, and AI-driven technologies.
-
Utilize specialist software for project management to keep tabs on performance indicators, resource allocation, and project progress in real time.
-
Automation in Production: By automating repetitive operations, you may decrease human error, increase productivity, and free up your team to work on more difficult projects.
-
Data analytics: Track performance and anticipate any issues, including equipment breakdown or production bottlenecks, before they arise.
8. Effectively Manage the Supply Chain
An essential part of every manufacturing endeavour is the supply chain. The timely, accurate, and cost-effective delivery of supplies and components is guaranteed by efficient supply chain management.
-
Vendor Relationships: Build trusting bonds with suppliers by making sure they are aware of the requirements and deadlines for your project.
-
Supply Chain Visibility: To obtain real-time supply chain visibility, leverage technologies such as blockchain and the Internet of Things. This facilitates cargo tracking, inventory level monitoring, and delay prediction.
-
Alternative Providers: Keep backup suppliers ready to go to prevent production delays brought on by shortages or problems with primary supplier delivery.
9. Communication is Essential
Multiple departments, including production, engineering, quality control, procurement, and more, are frequently involved in manufacturing projects. Everyone must agree with the project's objectives and present state for effective communication to occur.
-
Organize regular meetings on a daily or weekly basis to discuss any issues and assess the status of the project.
-
Cross-Departmental Cooperation: To handle issues and keep a constant workflow, promote cooperation across departments.
-
Use Communication Systems: To make sure that crucial updates and changes are accessible to all stakeholders, make use of project management systems that include integrated communication capabilities.
10. Track and Manage Development
After the project starts, it's critical to keep an eye on its development to make sure everything is proceeding as planned.
-
KPIs and Metrics: To gauge the performance of a project, use Key Performance Indicators (KPIs) such as production rates, defect rates, and on-time delivery.
-
Variance analysis compares the project's actual performance to its anticipated advancement. Consider the reason and make the necessary adjustments if there is a large variation.
-
Change management: Make sure all stakeholders are aware of any adjustments that may be required throughout the project and that they are well recorded. For more extensive projects, a change control board may be helpful.
What Project Management Tips for Manufacturing Projects Will Help in 2024?
By 2024, the industry of manufacturing is expected to continue to expand quickly, driven by advances in technology globalization and changing market demands. Effective project management is crucial for manufacturing companies to remain in the game, keep up with customer demands and remain profitable in a highly competitive market. The management techniques for project management in manufacturing that we discussed earlier are especially relevant to the current challenges and opportunities to come. This is how they could assist in 2024:
1. Aftencing to Technological Developments
-
Automation, as well as AI Automation robots, robotics as well as artificial intelligence (AI), become more integrated into manufacturing project management, and managers will need to incorporate the latest technologies in their processes. Tools that help manage projects that allow the real-time tracking of data, predictive analytics as well as automated processes, will be essential.
-
Industry 4.0: By 2024 the recurrent adoption of Industry 4.0 concepts will require plans for project management that manage intelligent production, connected systems with IoT devices. These technologies enhance visibility and decision-making capabilities, which makes precise planning and managing risk more crucial than ever before.
2. Disrupting the Supply Chain Disruptions
Supply disruptions to supply chains, which have become a frequent problem in recent times they will continue to affect manufacturing projects through 2024. Global supply chains are susceptible to geopolitical conflicts or natural disasters as well as economic turmoil.
-
Accessibility to Supply: Chain Utilizing technologies such as blockchain and IoT to enhance transparency in supply chains will help manufacturing companies reduce risks and ensure the timely delivery of the materials.
-
Diversifying suppliers: A backup supplier and sourcing from different locations will allow manufacturers to adapt quickly to any disruptions, thus avoiding costly delays to projects.
3. Reaching Sustainability Goals
Sustainability in the environment will play an increasingly important importance in manufacturing projects by 2024, as both governments and customers demand green methods of production and products.
-
Sustainable planning Project management techniques that are focused on cutting down on waste and maximizing energy consumption, like Lean manufacturing and production that is Just-in-Time are crucial in reaching sustainability goals.
-
green certifications The compliance to environmental standards and the acquisition of green certifications requires meticulous planning and allocation of resources and management of risk, project managers must ensure that their projects are in compliance with these requirements without causing more cost.
4. Improved Efficiency Using Lean and Agile Methodologies
In 2024, manufacturing projects will require greater flexibility to allow for shorter lifespans and the need for personalization.
-
Agile Manufacturing: Agile methods for managing projects enable teams to rapidly iterate adjust to changes and increase collaboration. This is crucial when manufacturers develop new products or upgrades to equipment.
-
Lean Manufacturing: The focus is on the reduction of waste, improving efficiency, and providing value to the consumer will continue to guide manufacturing initiatives. Lean manufacturing principles can help manufacturers keep their profits up while meeting customers' requirements for speed and quality.
5. Navigating Workforce Challenges
The industrial sector will continue to face challenges with its workforce such as talent shortages and the necessity of educating workers to work with advanced technologies.
-
Training and upskilling: Project managers need to ensure that their employees are educated to operate the latest equipment, control the automated process, as well as adjust to the latest technology. Training programs should be integrated into the project's timelines and budgets.
-
employee engagement: A clear and efficient communication strategy as well as delegation can improve the productivity of employee satisfaction. Maintaining skilled employees and keeping the morale of the team is crucial to the success of your project.
In summary
Manufacturing project management necessitates a delicate balancing act between time, resources, and quality control. Using the advice provided in this article, you may successfully manage the intricacies of manufacturing projects. These ideas range from defining clear goals and doing thorough planning to using technology and communicating effectively. These techniques will assist you in finishing projects on schedule, within budget, and to the greatest standards, regardless of whether you're working on a large-scale industrial effort or small-scale manufacturing.
Manufacturing project managers may maximise productivity and lower the possibility of delays or budget overruns by adopting concepts like lean manufacturing, continuous improvement, and risk management. Strong project management is crucial in the ever-changing manufacturing sector if you want to stay competitive, satisfy customers, and promote long-term success.
FAQ
Q1. How to manage a project in manufacturing?
Ans. Strategies for manufacturing project management
-
Step 1: Define Project Scope & Deliverables. Before diving into timelines, clearly define your project scope.
-
Step 2: Break Down the Project into Tasks.
-
Step 3: Estimate Task Durations.
-
Step 4: Identify Dependencies.
-
Step 5: Schedule Your Tasks.
-
Step 6: Communicate & Refine.
Q2. What is project management in a manufacturing company?
Ans. Project management helps ensure that quality standards are maintained throughout manufacturing, reducing the risk of errors and resulting in improved product quality and customer satisfaction.
Q3. What is the role of a project manager in manufacturing?
Ans. Creating a Workable Plan
-
Setting the parameters of the testing requirements.
-
Whether the project can meet the business's expectations in terms of value and returns.
-
Whether the project will meet the client's brief or expectations.
-
Objectives and deadlines to meet these objectives.
Q4. What is the project process in manufacturing?
Ans. Project Manufacturing is an operation designed to produce unique but similar products. It takes advantage of common manufacturing requirements (and therefore efficiencies) while allowing for customization into “unique” combinations. Unique orders may be managed like a project.
Q5. How do I become a manufacturing project manager?
Ans. Some companies prefer candidates with a bachelor's degree in a relevant field. Your previous work duties and responsibilities should help you understand how to organize and manage the many moving parts involved with a manufacturing project. These aspects include budgeting, scheduling, planning, and executing.